Challenges in the control of pharmaceutical manufacturing processes on paper
In many pharmaceutical companies, employees still record manufacturing control data on paper and authenticate it with their handwritten signature. This can lead to inefficiencies and errors that jeopardize data integrity.
As mentioned in previous articles, it is essential to document each step of the drug manufacturing process with the corresponding signature. This practice is not only essential but also mandatory in GMP-regulated environments, as it ensures the attributability and legibility of data, fundamental requirements derived from the principles of ALCOA+. For more information on this topic, you can refer to our article “Employees’ identification in the pharmaceutical industry according ALCOA+.”
The processes in drug manufacturing can take between half an hour and one hour to be completed, requiring approximately six signatures from operators, supervisors, and quality control personnel. On a standard 8-hour workday, this means that each workstation could perform up to 96 signature processes for process control and user identification.
Currently, the methods for collecting data and, consequently, identifying operators during process control, differ among pharmaceutical companies, adjusting to their technological and operational needs. Many companies still use non-digitized methods, which are based on manual recording of actions and identification of users using paper forms. In contrast, other companies have already evolved to digitized methods, using electronic signatures and specialized software (MES, ERP, EBR, LIMS) for efficient process and data management.
Next we will focus on process control and data collection under traditional methods.
How does the pharmaceutical industry carry out process control on paper?
The process begins with an initial stage, where a master planning document is created, such as the “manufacturing guide”, detailing the products to be manufactured, materials needed, and authorized processes. Planning covers both the long and short term, ensuring alignment and availability of equipment and personnel.
The quality assurance department prints the documentation and gives it to the supervisors, who are responsible for distributing it to the operators. Another option is for supervisors to print a previously validated guide, indicating that only the paper document will be used as a data collection tool during production.
Once in the hands of the operators, they fill out the documents with the data collected during the manufacturing process. At a minimum, they will need to handwrite, for each task, the location where it is being performed, the date and time of each task, additional requested data for each one, and identify with their handwritten signature.
Subsequently, the data goes through a review by the manufacturing area supervisor, who validates and approves its conformity. Then, the supervisor delivers the documentation to the quality assurance (QA) department for further review, and finally, the latter stores the information in the final repositories following an archiving plan.
This plan defines a set of policies, procedures and guidelines for efficient information management. It deals with various aspects, such as document classification, retention periods, storage methods, access controls, audits and other aspects related to document management.
It is mandatory for companies to perform internal audit drills at least once a year, to ensure data integrity and efficiency in the traceability of actions.That’s why a common practice in the storage process is to scan the documentation to have a digital version of it, and thus have a more efficient access to the information.
With respect to inspections by regulatory entities, it is important to know that they are currently carried out without prior notice, except for significant changes in facilities or products.
What is the format of the paper documentation?
The documentation associated with the process is concise and has a clear structure, consisting of a header and footer. The footer is crucial to ensure the physical integrity of the document when printed, reflecting the total number of pages. The header, on the other hand, includes essential information such as the name of the document and the source template code, with additional considerations if there are multiple versions of the same template.
The remaining content of the document focuses on particular tasks and specifications of the process, detailing steps from line clearance to equipment label verification. This content is presented in tabular format, providing spaces for operators to record vital information, such as equipment code, date and time of revision, start and end of each activity, and who performs it. This is where the action taken and operator identification are recorded
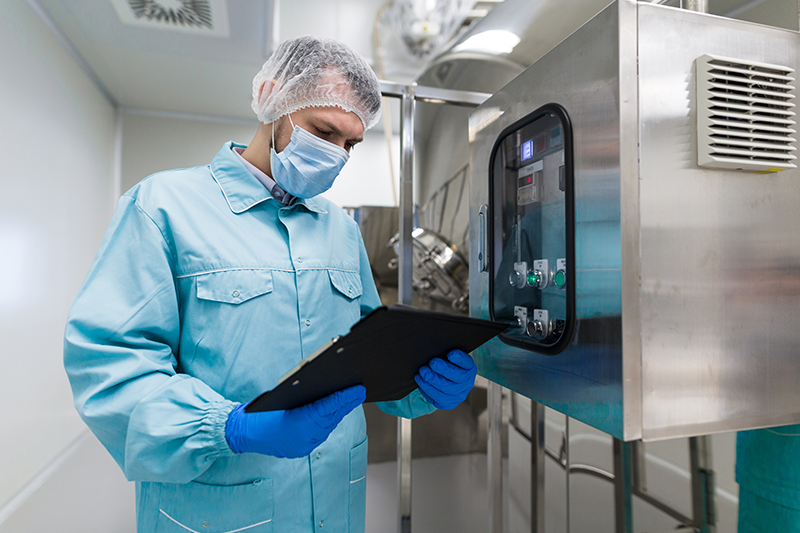
Risks associated with paper-based process control
The process detailed above can produce different inconveniences and/or risks that compromise the integrity of the data collected, and with it the compliance with the regulations. For example:
- Registration errors.
- Loss of forms and therefore of information.
- Manipulated records due to identity falsification.
- Unauthorized access to information.
- Outdated forms.
- Lack of accuracy in audits.
Additionally, we must take into account the inefficiencies due to the waste of employees’ time in successive handwritten notes over and over again, as well as in monitoring and searching for records in documentation stored on paper.
In future articles, we will go deeper into all of them.
How can these problems be avoided?
The solution is the digitization of processes, meaning the implementation and integration of specialized production control software, and the adoption of biometric electronic signatures for secure employee identification. You can find more detailed information in previous articles such as:
There are several specialized software for pharmaceutical manufacturing (ERP, MES, LIMS, EBR), which provide great value to the industry in the planning, implementation and control of processes, and thus greater efficiency and reduction of potential errors.
All these systems go far beyond digitizing the actions that are recorded with the employee’s electronic signature, automating many more processes. The fact that there are still many pharmaceutical companies that have not yet implemented them has to do with the economic costs and the time and dedication of their professionals for their deployment.
But there are ways to digitize the data recording process itself, with a simple, fast, and low-cost deployment, without waiting for manufacturing control software, as we explain in a later article.
Discover how Verazial ID Pharma can digitize the capture of all manufacturing data, and add the most advanced security with a biometric electronic signature.
Contact us for a demonstration and/or personalized study.
References
- Farmaceuticals employees [Taken from Freepik]
Challenges in the control of pharmaceutical manufacturing processes on paper
In many pharmaceutical companies, employees still record manufacturing control data on paper and authenticate it with their handwritten signature. This can lead to inefficiencies and errors that jeopardize data integrity.
As mentioned in previous articles, it is essential to document each step of the drug manufacturing process with the corresponding signature. This practice is not only essential but also mandatory in GMP-regulated environments, as it ensures the attributability and legibility of data, fundamental requirements derived from the principles of ALCOA+. For more information on this topic, you can refer to our article “Employees’ identification in the pharmaceutical industry according ALCOA+.”
The processes in drug manufacturing can take between half an hour and one hour to be completed, requiring approximately six signatures from operators, supervisors, and quality control personnel. On a standard 8-hour workday, this means that each workstation could perform up to 96 signature processes for process control and user identification.
Currently, the methods for collecting data and, consequently, identifying operators during process control, differ among pharmaceutical companies, adjusting to their technological and operational needs. Many companies still use non-digitized methods, which are based on manual recording of actions and identification of users using paper forms. In contrast, other companies have already evolved to digitized methods, using electronic signatures and specialized software (MES, ERP, EBR, LIMS) for efficient process and data management.
Next we will focus on process control and data collection under traditional methods.
How does the pharmaceutical industry carry out process control on paper?
The process begins with an initial stage, where a master planning document is created, such as the “manufacturing guide”, detailing the products to be manufactured, materials needed, and authorized processes. Planning covers both the long and short term, ensuring alignment and availability of equipment and personnel.
The quality assurance department prints the documentation and gives it to the supervisors, who are responsible for distributing it to the operators. Another option is for supervisors to print a previously validated guide, indicating that only the paper document will be used as a data collection tool during production.
Once in the hands of the operators, they fill out the documents with the data collected during the manufacturing process. At a minimum, they will need to handwrite, for each task, the location where it is being performed, the date and time of each task, additional requested data for each one, and identify with their handwritten signature.
Subsequently, the data goes through a review by the manufacturing area supervisor, who validates and approves its conformity. Then, the supervisor delivers the documentation to the quality assurance (QA) department for further review, and finally, the latter stores the information in the final repositories following an archiving plan.
This plan defines a set of policies, procedures and guidelines for efficient information management. It deals with various aspects, such as document classification, retention periods, storage methods, access controls, audits and other aspects related to document management.
It is mandatory for companies to perform internal audit drills at least once a year, to ensure data integrity and efficiency in the traceability of actions.That’s why a common practice in the storage process is to scan the documentation to have a digital version of it, and thus have a more efficient access to the information.
With respect to inspections by regulatory entities, it is important to know that they are currently carried out without prior notice, except for significant changes in facilities or products.
What is the format of the paper documentation?
The documentation associated with the process is concise and has a clear structure, consisting of a header and footer. The footer is crucial to ensure the physical integrity of the document when printed, reflecting the total number of pages. The header, on the other hand, includes essential information such as the name of the document and the source template code, with additional considerations if there are multiple versions of the same template.
The remaining content of the document focuses on particular tasks and specifications of the process, detailing steps from line clearance to equipment label verification. This content is presented in tabular format, providing spaces for operators to record vital information, such as equipment code, date and time of revision, start and end of each activity, and who performs it. This is where the action taken and operator identification are recorded
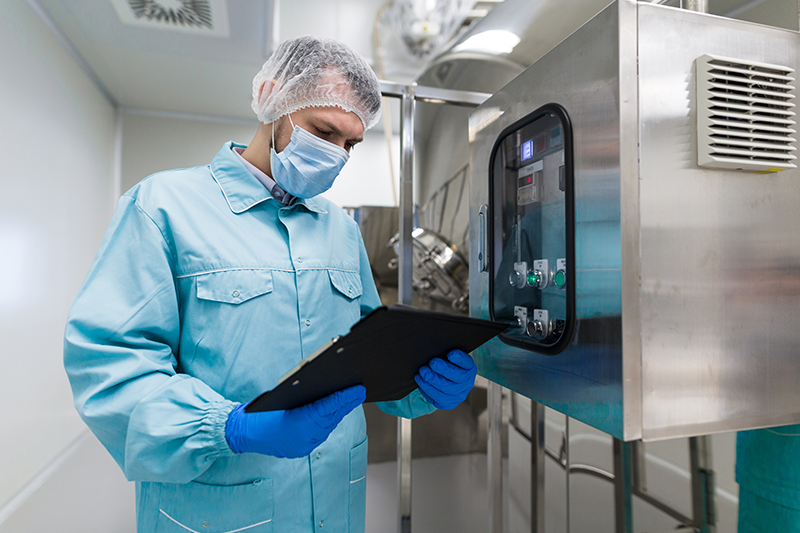
Risks associated with paper-based process control
The process detailed above can produce different inconveniences and/or risks that compromise the integrity of the data collected, and with it the compliance with the regulations. For example:
- Registration errors.
- Loss of forms and therefore of information.
- Manipulated records due to identity falsification.
- Unauthorized access to information.
- Outdated forms.
- Lack of accuracy in audits.
Additionally, we must take into account the inefficiencies due to the waste of employees’ time in successive handwritten notes over and over again, as well as in monitoring and searching for records in documentation stored on paper.
In future articles, we will go deeper into all of them.
How can these problems be avoided?
The solution is the digitization of processes, meaning the implementation and integration of specialized production control software, and the adoption of biometric electronic signatures for secure employee identification. You can find more detailed information in previous articles such as:
There are several specialized software for pharmaceutical manufacturing (ERP, MES, LIMS, EBR), which provide great value to the industry in the planning, implementation and control of processes, and thus greater efficiency and reduction of potential errors.
All these systems go far beyond digitizing the actions that are recorded with the employee’s electronic signature, automating many more processes. The fact that there are still many pharmaceutical companies that have not yet implemented them has to do with the economic costs and the time and dedication of their professionals for their deployment.
But there are ways to digitize the data recording process itself, with a simple, fast, and low-cost deployment, without waiting for manufacturing control software, as we explain in a later article.
Discover how Verazial ID Pharma can digitize the capture of all manufacturing data, and add the most advanced security with a biometric electronic signature.
Contact us for a demonstration and/or personalized study.
References
- Farmaceuticals employees [Taken from Freepik]
Challenges in the control of pharmaceutical manufacturing processes on paper
In many pharmaceutical companies, employees still record manufacturing control data on paper and authenticate it with their handwritten signature. This can lead to inefficiencies and errors that jeopardize data integrity.
As mentioned in previous articles, it is essential to document each step of the drug manufacturing process with the corresponding signature. This practice is not only essential but also mandatory in GMP-regulated environments, as it ensures the attributability and legibility of data, fundamental requirements derived from the principles of ALCOA+. For more information on this topic, you can refer to our article “Employees’ identification in the pharmaceutical industry according ALCOA+.”
The processes in drug manufacturing can take between half an hour and one hour to be completed, requiring approximately six signatures from operators, supervisors, and quality control personnel. On a standard 8-hour workday, this means that each workstation could perform up to 96 signature processes for process control and user identification.
Currently, the methods for collecting data and, consequently, identifying operators during process control, differ among pharmaceutical companies, adjusting to their technological and operational needs. Many companies still use non-digitized methods, which are based on manual recording of actions and identification of users using paper forms. In contrast, other companies have already evolved to digitized methods, using electronic signatures and specialized software (MES, ERP, EBR, LIMS) for efficient process and data management.
Next we will focus on process control and data collection under traditional methods.
How does the pharmaceutical industry carry out process control on paper?
The process begins with an initial stage, where a master planning document is created, such as the “manufacturing guide”, detailing the products to be manufactured, materials needed, and authorized processes. Planning covers both the long and short term, ensuring alignment and availability of equipment and personnel.
The quality assurance department prints the documentation and gives it to the supervisors, who are responsible for distributing it to the operators. Another option is for supervisors to print a previously validated guide, indicating that only the paper document will be used as a data collection tool during production.
Once in the hands of the operators, they fill out the documents with the data collected during the manufacturing process. At a minimum, they will need to handwrite, for each task, the location where it is being performed, the date and time of each task, additional requested data for each one, and identify with their handwritten signature.
Subsequently, the data goes through a review by the manufacturing area supervisor, who validates and approves its conformity. Then, the supervisor delivers the documentation to the quality assurance (QA) department for further review, and finally, the latter stores the information in the final repositories following an archiving plan.
This plan defines a set of policies, procedures and guidelines for efficient information management. It deals with various aspects, such as document classification, retention periods, storage methods, access controls, audits and other aspects related to document management.
It is mandatory for companies to perform internal audit drills at least once a year, to ensure data integrity and efficiency in the traceability of actions.That’s why a common practice in the storage process is to scan the documentation to have a digital version of it, and thus have a more efficient access to the information.
With respect to inspections by regulatory entities, it is important to know that they are currently carried out without prior notice, except for significant changes in facilities or products.
What is the format of the paper documentation?
The documentation associated with the process is concise and has a clear structure, consisting of a header and footer. The footer is crucial to ensure the physical integrity of the document when printed, reflecting the total number of pages. The header, on the other hand, includes essential information such as the name of the document and the source template code, with additional considerations if there are multiple versions of the same template.
The remaining content of the document focuses on particular tasks and specifications of the process, detailing steps from line clearance to equipment label verification. This content is presented in tabular format, providing spaces for operators to record vital information, such as equipment code, date and time of revision, start and end of each activity, and who performs it. This is where the action taken and operator identification are recorded
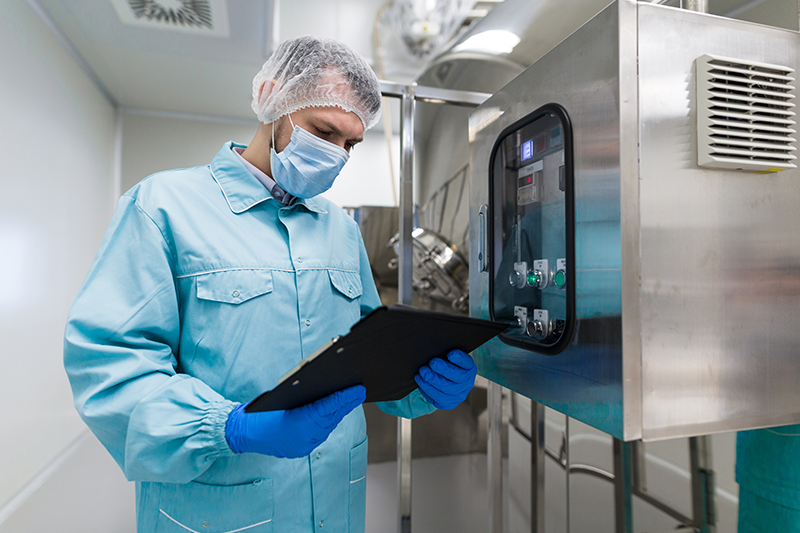
Risks associated with paper-based process control
The process detailed above can produce different inconveniences and/or risks that compromise the integrity of the data collected, and with it the compliance with the regulations. For example:
- Registration errors.
- Loss of forms and therefore of information.
- Manipulated records due to identity falsification.
- Unauthorized access to information.
- Outdated forms.
- Lack of accuracy in audits.
Additionally, we must take into account the inefficiencies due to the waste of employees’ time in successive handwritten notes over and over again, as well as in monitoring and searching for records in documentation stored on paper.
In future articles, we will go deeper into all of them.
How can these problems be avoided?
The solution is the digitization of processes, meaning the implementation and integration of specialized production control software, and the adoption of biometric electronic signatures for secure employee identification. You can find more detailed information in previous articles such as:
There are several specialized software for pharmaceutical manufacturing (ERP, MES, LIMS, EBR), which provide great value to the industry in the planning, implementation and control of processes, and thus greater efficiency and reduction of potential errors.
All these systems go far beyond digitizing the actions that are recorded with the employee’s electronic signature, automating many more processes. The fact that there are still many pharmaceutical companies that have not yet implemented them has to do with the economic costs and the time and dedication of their professionals for their deployment.
But there are ways to digitize the data recording process itself, with a simple, fast, and low-cost deployment, without waiting for manufacturing control software, as we explain in a later article.
Discover how Verazial ID Pharma can digitize the capture of all manufacturing data, and add the most advanced security with a biometric electronic signature.
Contact us for a demonstration and/or personalized study.
References
- Farmaceuticals employees [Taken from Freepik]
You May Also Like
You May Also Like