What are the disadvantages of using handwritten signatures in pharmaceutical process control?
In many pharmaceutical companies, employees record their manufacturing actions on paper with handwritten signatures, which creates risks and inefficiencies. It is possible to digitize these processes in a simple way and add the security of the biometric electronic signature.
The regulations in the manufacturing processes of the pharmaceutical industry require in GMP (Good Manufacturing Practices) environments to exhaustively record each manufacturing action, including the signature of the employee who performed it. Records must comply with the principles of attributability and legibility, fundamental principles of ALCOA+. For more details, please refer to our article “Employees’ identification in the pharmaceutical industry according ALCOA+”.
The current state of the industry reveals a diversity of methods for the control and recording of these signatures: from handwritten signatures recorded on paper to electronic signatures on specialized software (MES, ERP, EBR, LIMS).
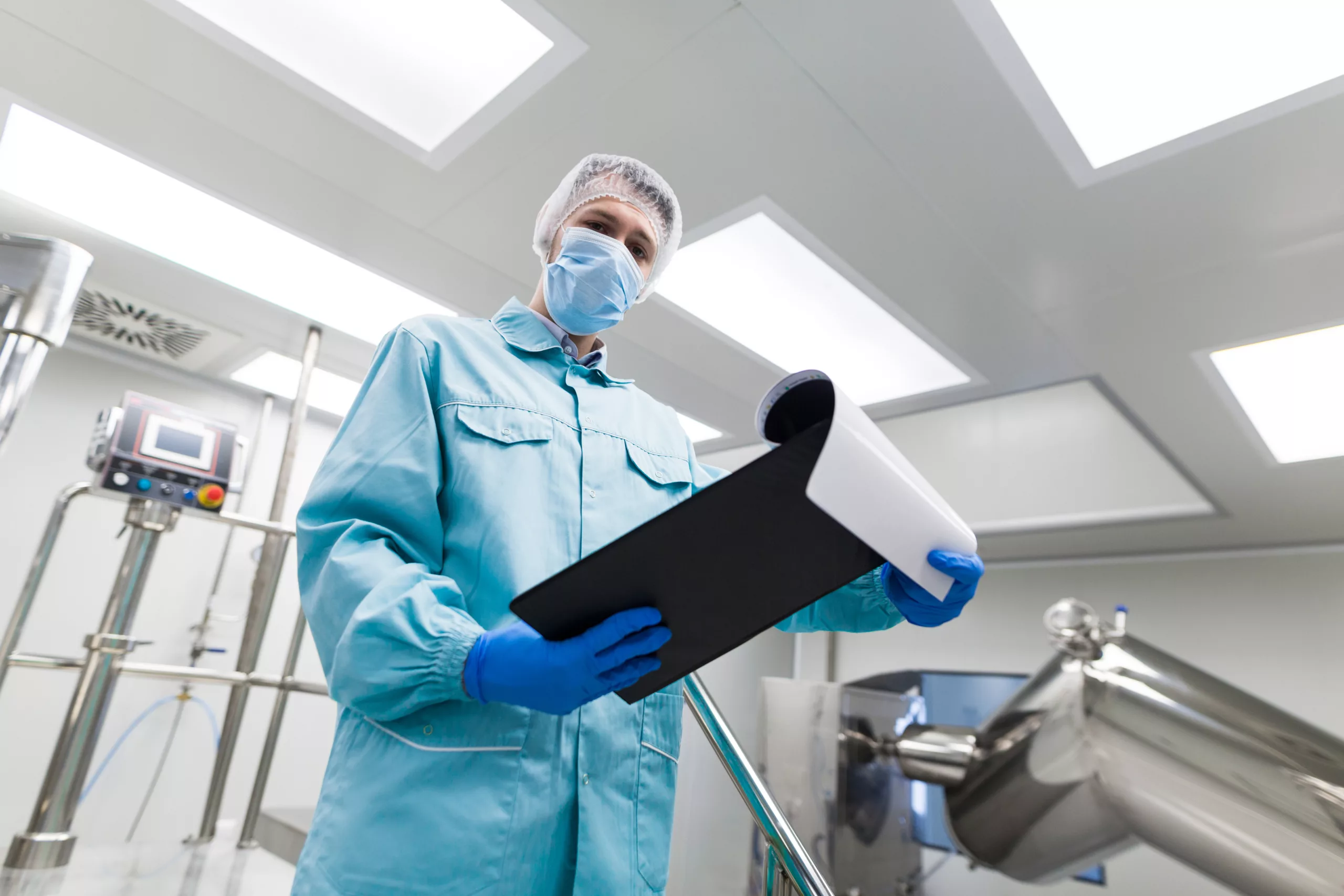
In a previous article, “Challenges in the control of pharmaceutical manufacturing processes on paper”, we detailed the process, the factors involved, and mentioned the risks inherent in this method, that are explained below.
Recording errors
Paper-based processes require employees to manually and consistently write a series of data such as date, time, location, and handwritten signature for each task performed. This involves additional work for employees, which is not only repetitive and tedious but also more prone to errors than automated processes. Such errors can manifest in the omission of critical details or the inclusion of incorrect information. All of this can have a significant impact on the accuracy and completeness of the data collected, weakening the validity of the records and potentially complicating decision making based on these data.
Loss of forms and information
The possibility of loss, irreparable damage or even accidental destruction of physical forms can lead to gaps in documentation, creating difficulties in traceability and compromising compliance with current regulations. This risk not only affects data integrity, but can also impact an organization’s ability to demonstrate compliance in GMP environments. For a more detailed discussion on regulatory and normative aspects, you can refer to our article “Manufacturing in the pharmaceutical industry: employees’ identification and data integrity “.
Records manipulated by identity fraud
As handwritten signatures are easy to forge, there is a risk of manipulating records, attributing activities to employees who did not perform them. This scenario not only compromises the reliability of data, but also undermines confidence in processes and the authenticity of operations, putting at risk the integrity of data, and with it, regulatory compliance.
Unauthorized access to information
Information stored on paper tends to be more exposed to unauthorized access. Since documents with data are manually transferred from one location to another, there is a greater risk of manipulation or alteration of the data, compromising the integrity of the information collected.
Outdated forms
The lack of rigorous version control increases the risk of confusion, since users can access outdated versions of the forms, unaware of crucial modifications. This not only leads to the omission of essential fields but also makes it possible to include incorrect information, compromising the accuracy of the records.
Lack of accuracy in audits
The likelihood of misplacement, errors in collection, manipulation or alteration, and misinformation resulting from the collection of paper-based data compromises the ability to respond to audits, exposing the company to serious penalties. This deficit in the integrity and authenticity of the information collected not only threatens operational continuity but can also undermine the company’s reputation in the pharmaceutical industry.
Inefficiency due to time loss
In pharmaceutical processes, the need for daily signatures involves repetitive manual notations, with up to 96 signature procedures per workstation in a standard 8-hour workday. Additionally, there is the task of overseeing and searching for records in paper-based documentation. These repetitive activities can lead to significant delays, affecting the efficiency and productivity of the entire process.
How can the risks associated with paper-based process control be eliminated?
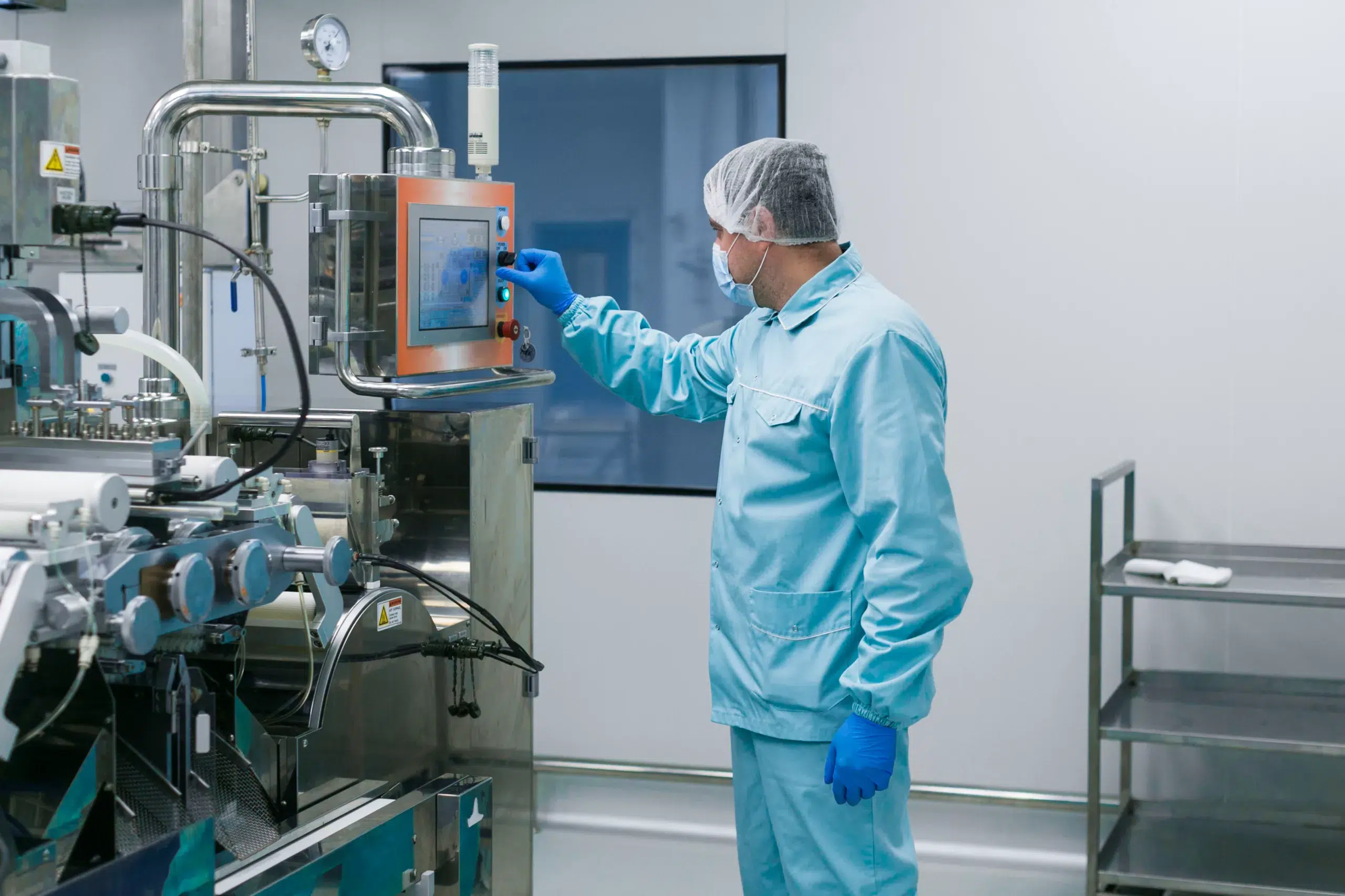
The solution involves the digitization of processes, i.e., implementing and integrating specialized production control software, with the implementation of biometric electronic signatures for the secure identification of employees. To learn more about this topic, please review our article Electronic signature in pharmaceutical manufacturing: Does it preserve data integrity and comply with regulations?.
The integration of production control software, such as ERPs (Enterprise Resource Planning), MES (Manufacturing Execution System), LIMS (Laboratory Information Management System) and EBR (Electronic Batch Record), represents an investment that brings great value to the industry in the planning, implementation and control of processes, and thus greater efficiency and reduction of potential errors.
It is important to consider that this investment not only involves the disbursement of financial resources, but also integration time, since each software must be fine-tuned and configured in a customized way to adapt to the specific manufacturing processes of each pharmaceutical company that continues to perform production control on paper.
However, it is possible to digitize the data collection process in production without waiting for the full value of manufacturing control software. And therefore both needs can be addressed separately. There are solutions with affordable costs and very fast deployment time that allow employees to report actions in the same way as they did on paper, but from a PC or mobile device.
The employee will no longer have to manually write the location or date and time for each action, as they will be automatically recorded in the system. There will be no paper handling, as all information will be digitized. This will result in significant improvements in terms of security, efficiency, data integrity assurance, and regulatory compliance.
Once the process has been digitized, we will be able to use the electronic signature, and enjoy the maximum security and convenience provided by the biometric electronic signature, as can be seen in our previous article “Biometric electronic signature in pharmaceutical manufacturing processes”.
Discover how Verázial ID Pharma offers you a comprehensive solution digitizing the collection of manufacturing data, and the most advanced security with a biometric electronic signature.
Contact us for a demonstration and/or personalized study.
What are the disadvantages of using handwritten signatures in pharmaceutical process control?
In many pharmaceutical companies, employees record their manufacturing actions on paper with handwritten signatures, which creates risks and inefficiencies. It is possible to digitize these processes in a simple way and add the security of the biometric electronic signature.
The regulations in the manufacturing processes of the pharmaceutical industry require in GMP (Good Manufacturing Practices) environments to exhaustively record each manufacturing action, including the signature of the employee who performed it. Records must comply with the principles of attributability and legibility, fundamental principles of ALCOA+. For more details, please refer to our article “Employees’ identification in the pharmaceutical industry according ALCOA+”.
The current state of the industry reveals a diversity of methods for the control and recording of these signatures: from handwritten signatures recorded on paper to electronic signatures on specialized software (MES, ERP, EBR, LIMS).
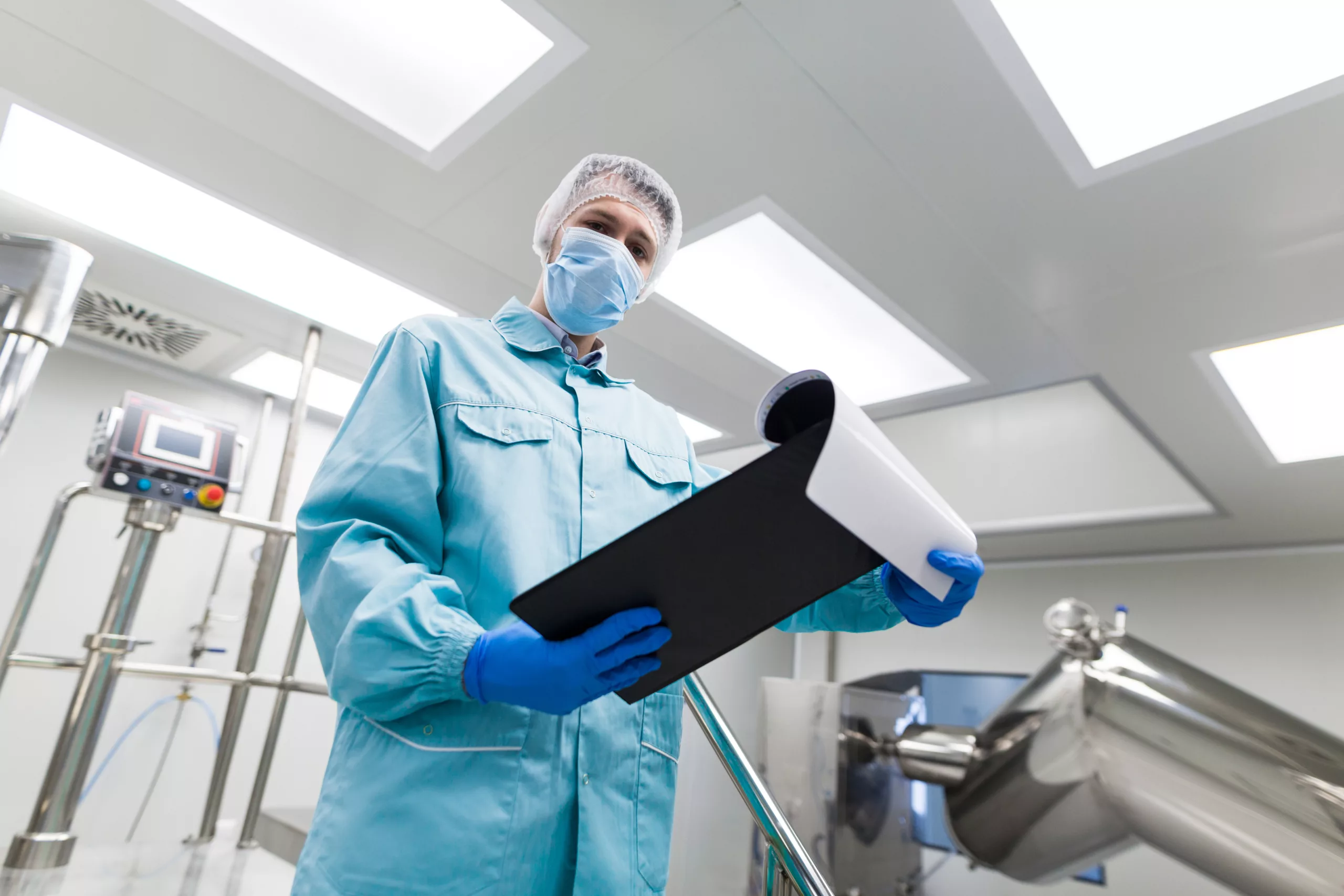
In a previous article, “Challenges in the control of pharmaceutical manufacturing processes on paper”, we detailed the process, the factors involved, and mentioned the risks inherent in this method, that are explained below.
Recording errors
Paper-based processes require employees to manually and consistently write a series of data such as date, time, location, and handwritten signature for each task performed. This involves additional work for employees, which is not only repetitive and tedious but also more prone to errors than automated processes. Such errors can manifest in the omission of critical details or the inclusion of incorrect information. All of this can have a significant impact on the accuracy and completeness of the data collected, weakening the validity of the records and potentially complicating decision making based on these data.
Loss of forms and information
The possibility of loss, irreparable damage or even accidental destruction of physical forms can lead to gaps in documentation, creating difficulties in traceability and compromising compliance with current regulations. This risk not only affects data integrity, but can also impact an organization’s ability to demonstrate compliance in GMP environments. For a more detailed discussion on regulatory and normative aspects, you can refer to our article “Manufacturing in the pharmaceutical industry: employees’ identification and data integrity “.
Records manipulated by identity fraud
As handwritten signatures are easy to forge, there is a risk of manipulating records, attributing activities to employees who did not perform them. This scenario not only compromises the reliability of data, but also undermines confidence in processes and the authenticity of operations, putting at risk the integrity of data, and with it, regulatory compliance.
Unauthorized access to information
Information stored on paper tends to be more exposed to unauthorized access. Since documents with data are manually transferred from one location to another, there is a greater risk of manipulation or alteration of the data, compromising the integrity of the information collected.
Outdated forms
The lack of rigorous version control increases the risk of confusion, since users can access outdated versions of the forms, unaware of crucial modifications. This not only leads to the omission of essential fields but also makes it possible to include incorrect information, compromising the accuracy of the records.
Lack of accuracy in audits
The likelihood of misplacement, errors in collection, manipulation or alteration, and misinformation resulting from the collection of paper-based data compromises the ability to respond to audits, exposing the company to serious penalties. This deficit in the integrity and authenticity of the information collected not only threatens operational continuity but can also undermine the company’s reputation in the pharmaceutical industry.
Inefficiency due to time loss
In pharmaceutical processes, the need for daily signatures involves repetitive manual notations, with up to 96 signature procedures per workstation in a standard 8-hour workday. Additionally, there is the task of overseeing and searching for records in paper-based documentation. These repetitive activities can lead to significant delays, affecting the efficiency and productivity of the entire process.
How can the risks associated with paper-based process control be eliminated?
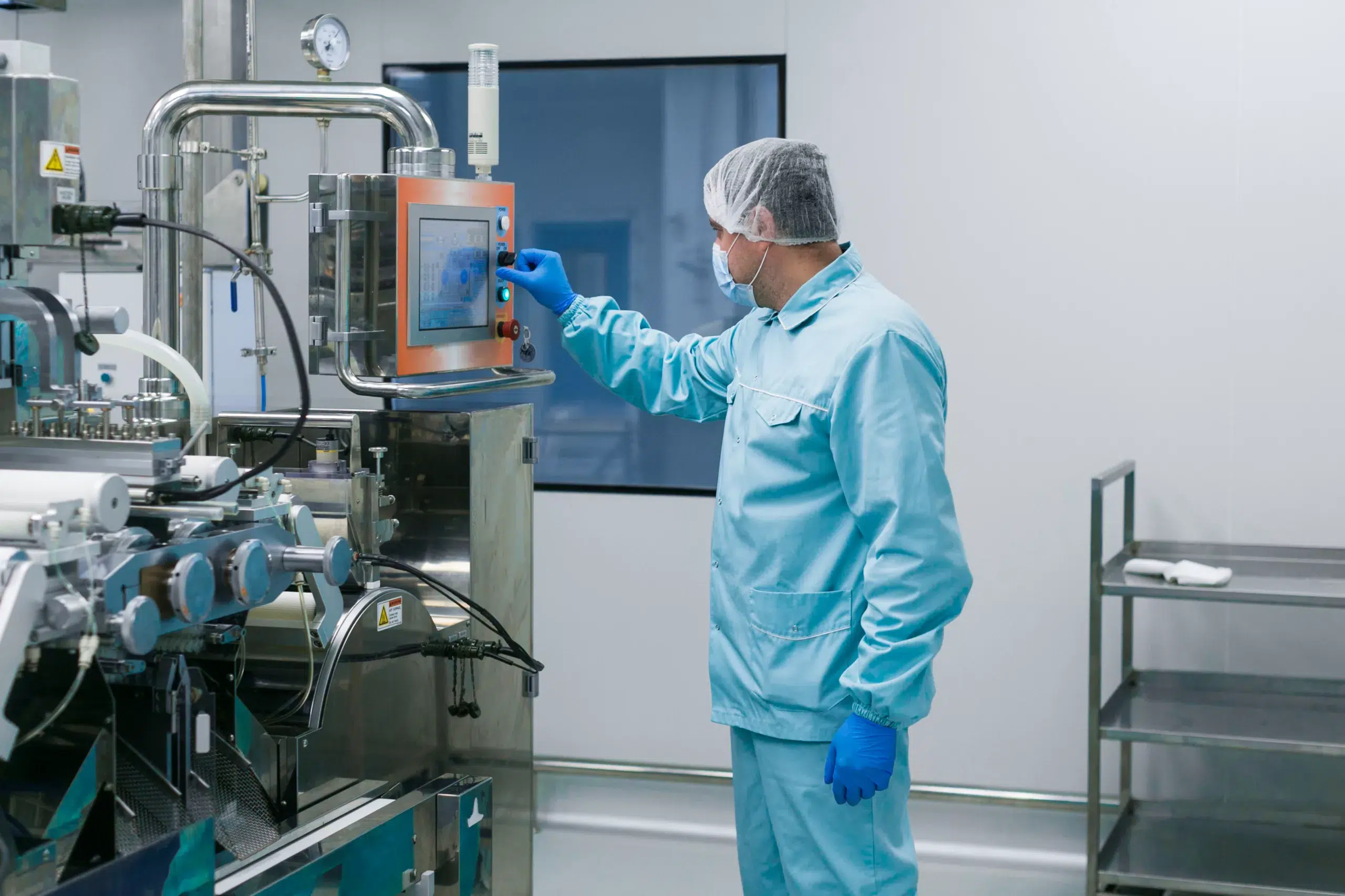
The solution involves the digitization of processes, i.e., implementing and integrating specialized production control software, with the implementation of biometric electronic signatures for the secure identification of employees. To learn more about this topic, please review our article Electronic signature in pharmaceutical manufacturing: Does it preserve data integrity and comply with regulations?.
The integration of production control software, such as ERPs (Enterprise Resource Planning), MES (Manufacturing Execution System), LIMS (Laboratory Information Management System) and EBR (Electronic Batch Record), represents an investment that brings great value to the industry in the planning, implementation and control of processes, and thus greater efficiency and reduction of potential errors.
It is important to consider that this investment not only involves the disbursement of financial resources, but also integration time, since each software must be fine-tuned and configured in a customized way to adapt to the specific manufacturing processes of each pharmaceutical company that continues to perform production control on paper.
However, it is possible to digitize the data collection process in production without waiting for the full value of manufacturing control software. And therefore both needs can be addressed separately. There are solutions with affordable costs and very fast deployment time that allow employees to report actions in the same way as they did on paper, but from a PC or mobile device.
The employee will no longer have to manually write the location or date and time for each action, as they will be automatically recorded in the system. There will be no paper handling, as all information will be digitized. This will result in significant improvements in terms of security, efficiency, data integrity assurance, and regulatory compliance.
Once the process has been digitized, we will be able to use the electronic signature, and enjoy the maximum security and convenience provided by the biometric electronic signature, as can be seen in our previous article “Biometric electronic signature in pharmaceutical manufacturing processes”.
Discover how Verázial ID Pharma offers you a comprehensive solution digitizing the collection of manufacturing data, and the most advanced security with a biometric electronic signature.
Contact us for a demonstration and/or personalized study.
What are the disadvantages of using handwritten signatures in pharmaceutical process control?
In many pharmaceutical companies, employees record their manufacturing actions on paper with handwritten signatures, which creates risks and inefficiencies. It is possible to digitize these processes in a simple way and add the security of the biometric electronic signature.
The regulations in the manufacturing processes of the pharmaceutical industry require in GMP (Good Manufacturing Practices) environments to exhaustively record each manufacturing action, including the signature of the employee who performed it. Records must comply with the principles of attributability and legibility, fundamental principles of ALCOA+. For more details, please refer to our article “Employees’ identification in the pharmaceutical industry according ALCOA+”.
The current state of the industry reveals a diversity of methods for the control and recording of these signatures: from handwritten signatures recorded on paper to electronic signatures on specialized software (MES, ERP, EBR, LIMS).
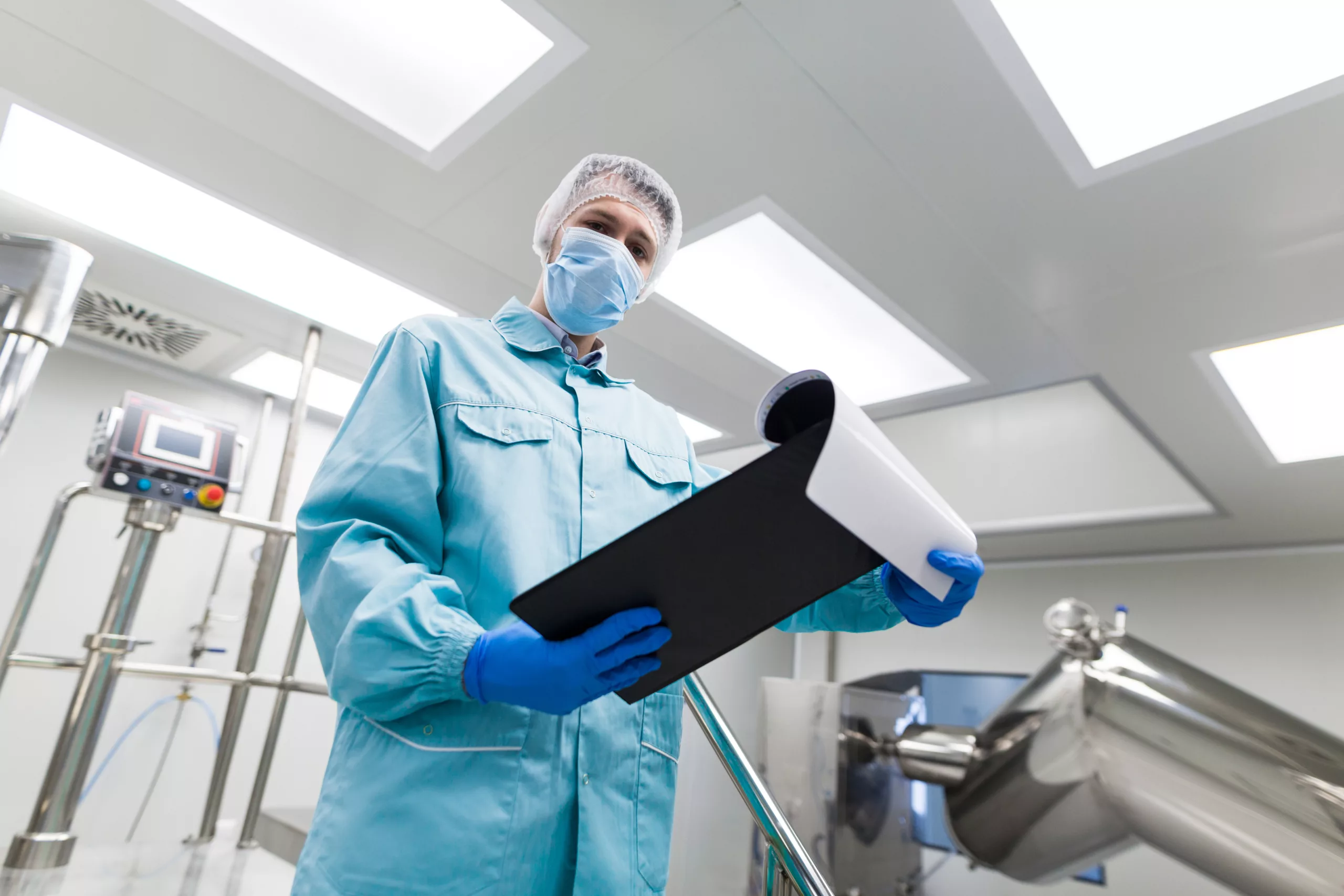
In a previous article, “Challenges in the control of pharmaceutical manufacturing processes on paper”, we detailed the process, the factors involved, and mentioned the risks inherent in this method, that are explained below.
Recording errors
Paper-based processes require employees to manually and consistently write a series of data such as date, time, location, and handwritten signature for each task performed. This involves additional work for employees, which is not only repetitive and tedious but also more prone to errors than automated processes. Such errors can manifest in the omission of critical details or the inclusion of incorrect information. All of this can have a significant impact on the accuracy and completeness of the data collected, weakening the validity of the records and potentially complicating decision making based on these data.
Loss of forms and information
The possibility of loss, irreparable damage or even accidental destruction of physical forms can lead to gaps in documentation, creating difficulties in traceability and compromising compliance with current regulations. This risk not only affects data integrity, but can also impact an organization’s ability to demonstrate compliance in GMP environments. For a more detailed discussion on regulatory and normative aspects, you can refer to our article “Manufacturing in the pharmaceutical industry: employees’ identification and data integrity “.
Records manipulated by identity fraud
As handwritten signatures are easy to forge, there is a risk of manipulating records, attributing activities to employees who did not perform them. This scenario not only compromises the reliability of data, but also undermines confidence in processes and the authenticity of operations, putting at risk the integrity of data, and with it, regulatory compliance.
Unauthorized access to information
Information stored on paper tends to be more exposed to unauthorized access. Since documents with data are manually transferred from one location to another, there is a greater risk of manipulation or alteration of the data, compromising the integrity of the information collected.
Outdated forms
The lack of rigorous version control increases the risk of confusion, since users can access outdated versions of the forms, unaware of crucial modifications. This not only leads to the omission of essential fields but also makes it possible to include incorrect information, compromising the accuracy of the records.
Lack of accuracy in audits
The likelihood of misplacement, errors in collection, manipulation or alteration, and misinformation resulting from the collection of paper-based data compromises the ability to respond to audits, exposing the company to serious penalties. This deficit in the integrity and authenticity of the information collected not only threatens operational continuity but can also undermine the company’s reputation in the pharmaceutical industry.
Inefficiency due to time loss
In pharmaceutical processes, the need for daily signatures involves repetitive manual notations, with up to 96 signature procedures per workstation in a standard 8-hour workday. Additionally, there is the task of overseeing and searching for records in paper-based documentation. These repetitive activities can lead to significant delays, affecting the efficiency and productivity of the entire process.
How can the risks associated with paper-based process control be eliminated?
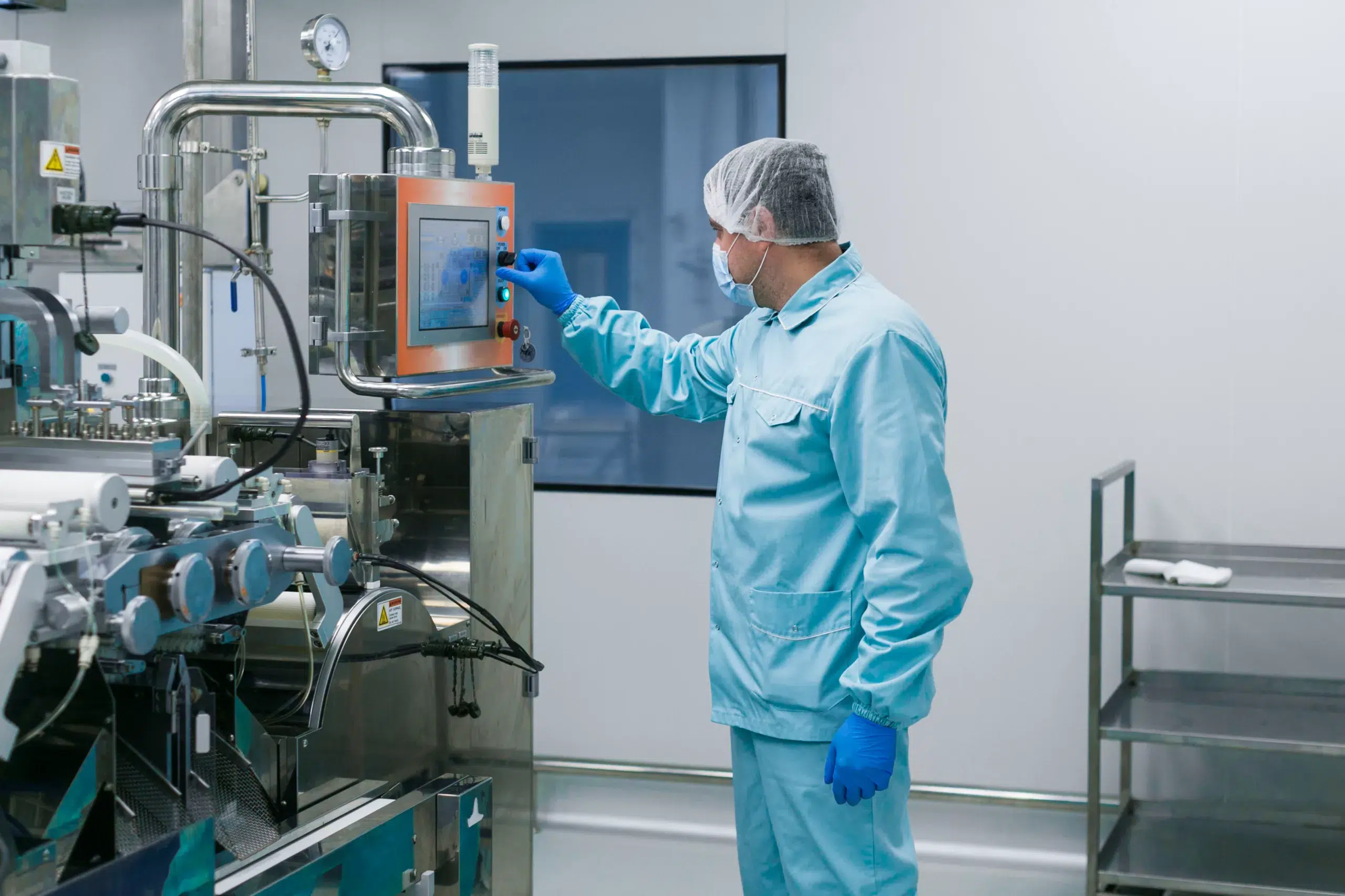
The solution involves the digitization of processes, i.e., implementing and integrating specialized production control software, with the implementation of biometric electronic signatures for the secure identification of employees. To learn more about this topic, please review our article Electronic signature in pharmaceutical manufacturing: Does it preserve data integrity and comply with regulations?.
The integration of production control software, such as ERPs (Enterprise Resource Planning), MES (Manufacturing Execution System), LIMS (Laboratory Information Management System) and EBR (Electronic Batch Record), represents an investment that brings great value to the industry in the planning, implementation and control of processes, and thus greater efficiency and reduction of potential errors.
It is important to consider that this investment not only involves the disbursement of financial resources, but also integration time, since each software must be fine-tuned and configured in a customized way to adapt to the specific manufacturing processes of each pharmaceutical company that continues to perform production control on paper.
However, it is possible to digitize the data collection process in production without waiting for the full value of manufacturing control software. And therefore both needs can be addressed separately. There are solutions with affordable costs and very fast deployment time that allow employees to report actions in the same way as they did on paper, but from a PC or mobile device.
The employee will no longer have to manually write the location or date and time for each action, as they will be automatically recorded in the system. There will be no paper handling, as all information will be digitized. This will result in significant improvements in terms of security, efficiency, data integrity assurance, and regulatory compliance.
Once the process has been digitized, we will be able to use the electronic signature, and enjoy the maximum security and convenience provided by the biometric electronic signature, as can be seen in our previous article “Biometric electronic signature in pharmaceutical manufacturing processes”.
Discover how Verázial ID Pharma offers you a comprehensive solution digitizing the collection of manufacturing data, and the most advanced security with a biometric electronic signature.
Contact us for a demonstration and/or personalized study.
You May Also Like
You May Also Like